Abstract
You can print anything... or can you? 3D printing is an exciting new technology that promises to very quickly create anything people can design. Scientists who want to make soft robots, like Baymax from Big Hero 6TM, are excited about 3D printers. Our team uses 3D printing to make molds to produce soft robots. Molding is like using a muffin tin to make cupcakes. But can you make anything with 3D printing or are there times when 3D-printed molds do not work? Just like a cupcake liner, 3D-printed molds leave ridges, like a Ruffles potato chip, in soft robots. These ridges are a weak point where cracks can form, causing the robot to pop like a balloon. To prevent this, we sometimes need to make our robots using very smooth molds made from metal. This article talks about when and how 3D printing is useful in making soft robots.
What is a Soft Robot
Have you ever seen a soft robot? They are a new type of robot that moves when they are inflated, like a balloon or Baymax from Big Hero 6TM! Unlike a balloon, soft robots have all sorts of purposes, which means they come in various shapes and sizes. When scientists have a goal in mind for a soft robot, they must make some prototypes to see if their idea works. Prototypes are a quick and inexpensive way to test many ideas. 3D printers allow scientists to make prototypes quickly. In this article, you will learn about 3D-printed molds and how scientists called soft roboticists use them to make soft robots. The type of printer we will talk about works by melting plastic and squeezing it through a little nozzle, like a hot glue gun melting sticks of glue. For examples of other types of 3D printing, see this article or [1]. In 3D printing, computer code tells the nozzle to move around above a flat surface, to lay down long strings of melted plastic to make a specified shape.
What is 3D Printing and How is it Used to Make Soft Robots?
Why is 3D printing useful? Well, 3D printers can make an idea into a real object very quickly and cheaply. Before 3D printing, making things involved taking a block of something like plastic or metal and cutting it with a machine, kind of like a stone carver or woodworker would. This is called subtractive manufacturing, or machining, because it subtracts material from the original block. 3D printing is a type of additive manufacturing. When a design is made for the first time, subtractive manufacturing can take days or weeks and cost quite a lot. If soft roboticists use 3D printers to make soft robots, they can change their designs quickly. They might discover that the skin of the robot they just made is so thin that it pops. With 3D printing, they just thicken the skin in the design on the computer, send it to the printer, and work on something else while it prints. Some designs finish printing in just a few hours. But what do soft roboticists print?
Some soft roboticists directly print their soft robots. This is similar to how the researchers in this article directly printed their structures. They have special printers that can print very soft materials. Some of the shapes our group of soft roboticists make do not work on these printers though, so our team and most other soft roboticists do not directly print our soft robots. Instead, we print molds [2, 3]. A mold is something that we can pour or squeeze material into to make the object we want. You might have used a mold to make Play-Doh into a shape, seen someone mold chocolate in the shape of a rabbit, or put sand into a bucket to mold it into a castle. Because we 3D print the molds used to make our robots, they can be in any shape we desire. Like pouring batter into a cake pan to bake, we pour liquid rubber into a mold and then let it solidify. Instead of baking the rubber, the process is called curing. Once the liquid rubber has cured, we open the mold and take out the robot. The most popular rubber used to make soft robots is silicone rubber, a cheap rubber that can stretch to 10 times its original size! Silicone rubber is used in products like cooking spatulas and even baby pacifiers.
When is 3D Printing not Useful?
While 3D printing is very useful for soft roboticists, it does have downsides. 3D printers squeeze out plastic in lines and use those lines to form layers, as in Figure 1. This leads to the 3D-printed mold having a rough surface when you look closely (Figure 2A). Just like how the ridges on a muffin liner give a muffin its ridges, our 3D-printed molds give our soft robots a rough surface that you can see when you look very closely. This is because the imprint of the 3D-printed lines and layers that make up the mold is left behind on the robot. This makes the walls weaker and more likely to break in some way or even pop (Figure 2C) [4]. To understand this, print out and follow the instructions in Figure 3. The paper with a small cut in it was much easier to break, right? It should have torn apart at the cut. This is because it is easier to lengthen a small tear than to start a new one. These tears can happen all at once, like with your pieces of paper, or slowly over time, as our robots are inflated and deflated over and over. This is the reason why the ends of ketchup packets are shaped like saw teeth. Each “V” shape is a place where a tear can easily start, making the ketchup packet easier to open. This is the largest drawback of using 3D-printed molds for soft robots: the ridges left by the 3D printer give tears a place to start. As you can see in Figure 2B the skin of a soft robot made from a 3D-printed mold can look a lot like the end of a ketchup packet.
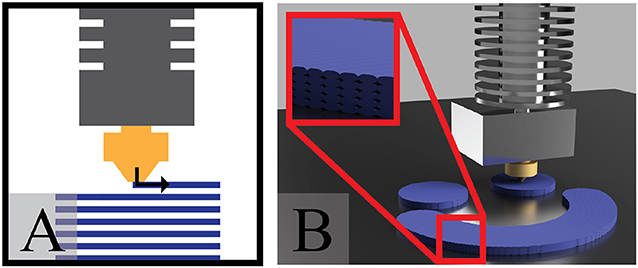
- Figure 1 - (A) 3D-printed layer lines being squeezed out of a heated printing nozzle.
- (B) How lines of plastic are connected to make layers and form objects. The red boxes show a zoomed region so that you can see layers and lines more easily.
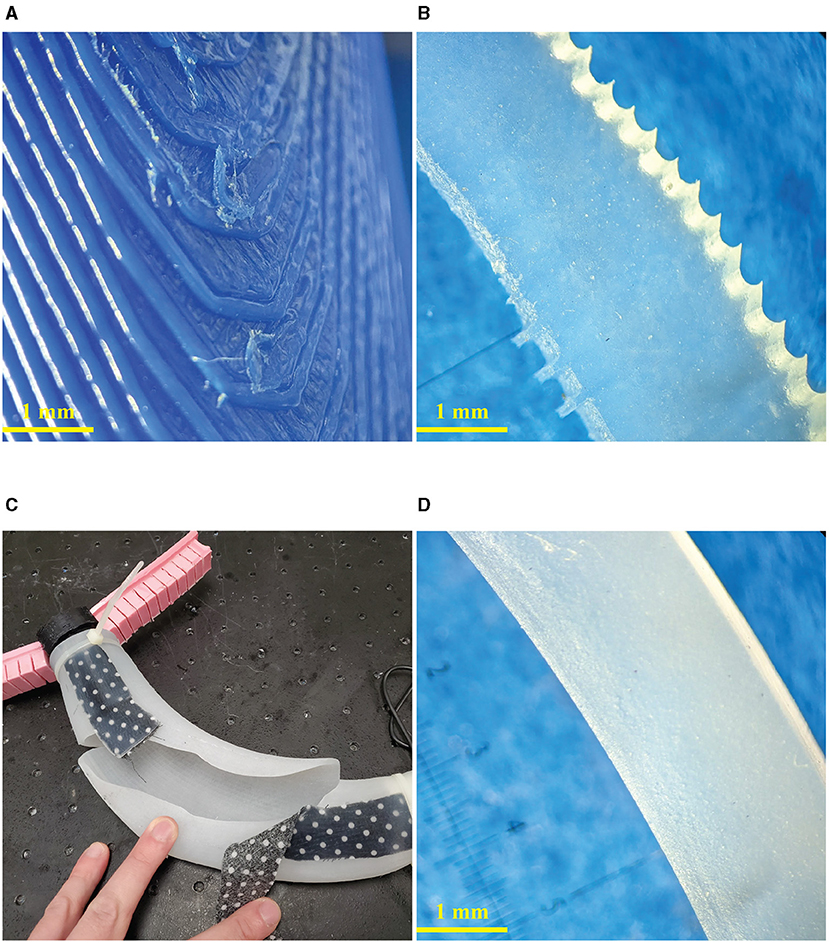
- Figure 2 - (A) A part of one of our 3D-printed soft robot molds.
- (B) A small cut-out portion of a soft robot made in a 3D printed mold. (C) A soft robot made in a 3D printed mold that has popped due to a crack starting at a layer line. (D) A small cut-out portion of a soft robot made in a machined mold.
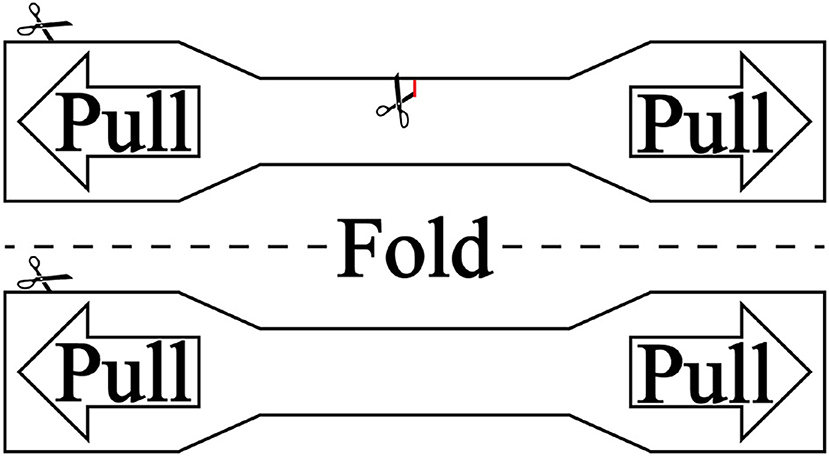
- Figure 3 - Print and cut out this image.
- Cut one of these shapes along the red line to represent a small tear or one of the ridges that our 3D-printed molds leave behind. Grab each end of one of the shapes and pull until it rips apart (try not to bend or twist it). Repeat with the other shape and notice the difference. These are called dogbone tensile specimens, and we use them a lot to test material strength. So, you are performing an experiment we do in our lab, except that we use a machine to pull our materials apart.
How Else Can We Make Our Molds?
If we cannot 3D-print our mold, what can we do? Remember subtractive manufacturing from the start of this article? This is exactly what our team uses [5]! With the help of automated machinery and precise tools, we machine a block of metal into a mold. This kind of subtractive manufacturing is more accurate than 3D printing, but more importantly, produces molds with much smoother surfaces. In Figures 2B, D, the soft robot made with a metal mold is much smoother than the robot made in a 3D-printed mold. Another advantage of metal molds is that they can produce more consistent robots. While every soft robot made from a single mold will be slightly different, the metal mold produces much more consistent robots than 3D-printed molds. As we mentioned at the beginning, cutting a mold out of a metal block is expensive and takes time, so we make a 3D-printed mold first to test our idea. We can then make changes to the mold and print another. We keep doing that until we have the design figured out. The robots made in the 3D-printed molds work well enough to figure out what changes need to be made to the mold design. Once the design is figured out, we spend the money and time to machine a metal mold. This means that, at first, we can quickly find and fix any problems in our design before spending the resources to make a metal mold for a stronger robot.
How Could You Make a Soft Robot
3D printing is a useful technology for soft roboticists. It allows them to try many designs quickly without spending a lot of time and money. It is not perfect—the defects it leaves in soft robots make them weaker. Because of this, we often 3D print our first few mold designs, and then machine a mold once we are done making changes. If you want to get started designing and making things, there are lots of options. First, when we design something, we use a computer program that lets us turn drawings into 3D shapes. This is called computer modeling. Fusion 360 is a free modeling program that you can use to design anything you want. We use programs like Fusion 360 to design our soft robot molds, but you could make anything, including something that no one has ever thought of before! Another program called a slicer slices the model into layers and tells the 3D printer where to put plastic. Many libraries and schools have 3D printers. You can print your designs there. There might also be a shop that does machining in your town that is willing to give you a tour. The field of soft robotics is constantly improving, with so much room for creative designs and solutions. Now that you know a little bit about how they are made, perhaps you will use the methods we have described to make and improve upon your own soft robot!
Glossary
Soft Robot: ↑ A robot that is flexible like an octopus as opposed to traditional robots that are made of hard segments like a beetle.
Prototype: ↑ An initial design or a few designs that help engineers test their ideas without spending the time and money to build the final product. A good example would be making a building out of cardboard to see how it looks before you make the actual building.
Mold: ↑ A mold is any empty object that you can fill to create an object with some desired shape. Some examples are Play-Doh molds, molds used to make chocolate rabbits, and buckets for making sand castles.
Soft Roboticist: ↑ Someone who builds and researches soft robots.
Subtractive Manufacturing: ↑ The process of creating a part by cutting raw material away.
Machine: ↑ Another term for subtractive manufacturing. To machine something is to cut down a material into a desired shape.
Additive Manufacturing: ↑ The process of creating a part by building it up from raw material.
Curing: ↑ This is when two liquid materials are put together and slowly become solid. This process is not drying (water leaving a liquid). Instead, there is a chemical change that happens when the two liquids are put together which makes them become a solid. You may have seen this with two-part glues like Gorilla glue.
Conflict of Interest
The authors declare that the research was conducted in the absence of any commercial or financial relationships that could be construed as a potential conflict of interest.
AI Tools Statement
Limited use of Open AI ChatGPT 3.5 was made to generate lists of ideas such as “Where would kids have encountered molding processes in everyday life?”. Most of these ideas were rejected, but the sand bucket analogy was kept.
Acknowledgments
Thank you to Cora for your suggestions and edits on how to make this manuscript accessible and enjoyable for the target audience. This work was supported by the National Science Foundation through grant number: 1935312.
References
[1] ↑ Wong, K. V., and Hernandez, A. 2012. A review of additive manufacturing. ISRN Mech. Eng. 2012:208760. doi: 10.5402/2012/208760
[2] ↑ Ilievski, F., Mazzeo, A. D., Shepherd, R. F., Chen, X., and Whitesides, G. M. 2011. Soft robotics for chemists. Angewandte Chemie Int. Ed. 50:1890–5. doi: 10.1002/anie.201006464
[3] ↑ Shepherd, R. F., Ilievski, F., Choi, W., Morin, S. A., Stokes, A. A., Mazzeo, A. D., et al. 2011. Multigait soft robot. Proc. Natl. Acad. Sci. U. S. A. 108:20400–3. doi: 10.1073/pnas.1116564108
[4] ↑ Bui, P. D. H., Prugh, B., Padilla, A. M. E., Schell, C., Keller, M., and Schultz, J. A. 2023. Endurance tests for a fabric reinforced inflatable soft actuator. Front. Mater. 10:1112540. doi: 10.3389/fmats.2023.1112540
[5] ↑ Williamson, J. G., and Schultz, J. 2023. “Stretchable optical waveguide sensor suitability for wrinkle degree detection in soft robots”, in 2023 IEEE International Conference on Soft Robotics (RoboSoft) (Singapore). p. 1–6.