Abstract
Robot arms can be found in many factories around the world. From the tiniest chip in a phone to the body of a car, robots are responsible for moving things around thousands of times a day. However, robots find themselves a bit stuck when dealing with more natural objects, such as fruits or vegetables. Their rigid bodies feel out of place amongst all the squishiness and different shapes and sizes of nature. One way to help solve that is by making robots softer. Soft grippers allow robots to delicately touch the world around them, grabbing fragile objects almost as easily as humans do. Many robots made of soft materials, called soft robots, are inspired by nature to help them interact with their environments. With hands made of softer materials, these robots are ready to help us not just in factories, but also in our daily lives. How are soft grippers created? What do they look like? In this article, we will explore the captivating realm of soft grippers!
Soft Grippers
Imagine you are in a factory—what do you see around you? You might picture robots and machines doing their best to help human workers make things. Now zoom in and imagine what these robots are actually doing.
Many robots in factories do what is called “pick and place” operations—taking objects from one place and delivering them somewhere else. Robots need good hands to do this work. So, what kind of hands should a robot have? One answer might be that they should have hands just like ours.
Unfortunately, human hands are surprisingly complex, and good human-like robot hands are still only seen in movies. Robots in factories may only need to perform some of the tasks our human hands can do, so robot creators might want simpler and cheaper hands, which are called grippers. A typical robot gripper consists of just two fingers; you can recreate one by pinching your thumb and index finger together. It is pretty simple and effective.
While rigid pinching robot grippers are strong and great for car parts and steel beams (Figure 1A), they can make it difficult for robots to pick up delicate objects, like fruits and vegetables.
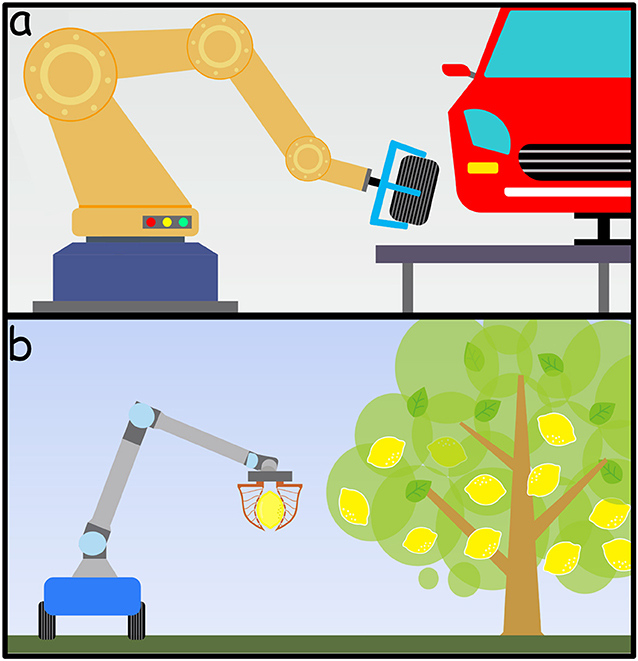
- Figure 1 - Robot arms and grippers doing their thing.
- (A) An industrial robot arm with a rigid gripper, assembling a car. (B) A smaller robot arm on wheels picking fruit with a soft gripper.
While you can hold lemons gently in your hand, a typical robot gripper must pinch fruit like lemons hard enough to pick them up, which could damage them. Humans can also bend their fingers around the lemons, and human skin applies just enough contact so that the lemons are held firmly. These abilities are key aspects of a new type of gripper called soft grippers.
Today, there are a lot of soft grippers, each unique in its design and abilities, and some are used in real-world applications (Figure 1B). In this article, we have compiled some examples of the most interesting soft grippers developed to date, highlighting their vast potential and usefulness in various tasks. More importantly, you will see how scientific inventions can be born from observing the world around us.
Finding Function From Fingers, Floaties, and Fish Fins
The first “soft robots” looked quite similar to your fingers, if your fingers had 10 times more joints. These were called continuum robots, and just like our fingers, scientists used muscle-like tendons and cables to bend them. So, continuum robots had a series of rigid links connected by bendable soft joints (Figure 2A). The joints can flop around as long the cable has no tension on it, but when engineered correctly, these human-like robot hands are strong and flexible.
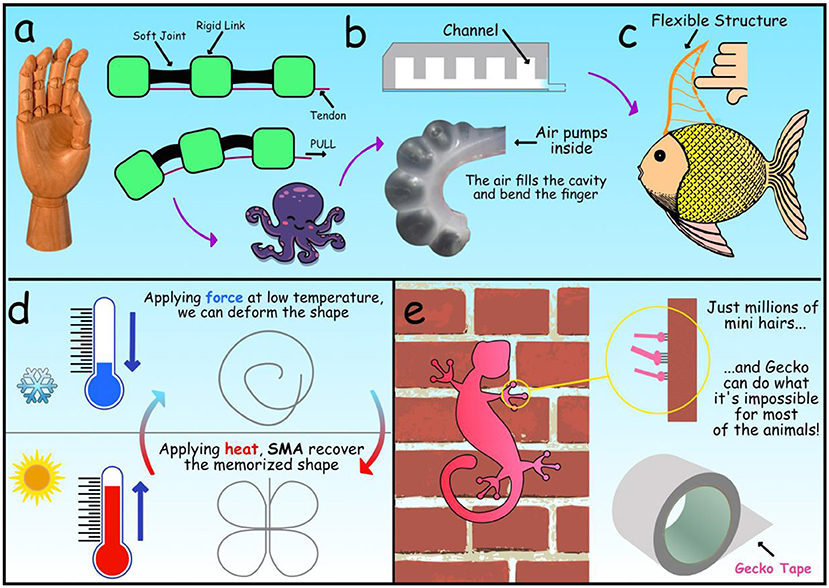
- Figure 2 - Soft grippers inspired by nature.
- (A) Robots can replicate the human hand by using a chain of rigid links and soft joints. Pulling on the tendon makes the robot “finger” bend. (B) The most common soft pneumatic gripper is like an octopus tentacle. It bends when it is inflated. (C) The fish fin was the inspiration for fin ray effect soft grippers. (D) SMAs change shape under different temperatures. (E) Geckos’ feet have microscopic structures that let them defy gravity. These structures led to the creation of Gecko Tape.
But what if we want to replicate something softer and natural looking, like an octopus tentacle? Tentacles do not have links and joints, which means that when they bend, there is no main bending point—they just curve. To replicate a tentacle structure, robot creators can make an enclosed pocket of air that deforms a certain way when you change the amount of air in it. A balloon or pool floatie could be considered a soft robot if it expands a certain way when it is inflated. These soft grippers are based on the principle of pneumatic networks (or PneuNets), through which pumping air into a “finger” structure causes it to bend in a desired way. If these fingers are arranged into pairs, trios, or more, a typical soft gripper is created (Figure 2B).
In 1997, a biologist named Leif Kniese was studying how fish moved, and he noticed that fish tails have a unique bone structure. When water (or a finger) pushes against a fish tail, it bends inwards (toward your finger) instead of bending away like a piece of paper would. This phenomenon, which helps fish control the flow of water around them, was later used in robot grippers. Called fin ray effect grippers (Figure 2C), these robot fingers simply surround objects they touch. When combined with a soft material, fin ray grippers are a great example of soft grippers, improving the usefulness of two-fingered grippers by making the fingers softer and smarter. In contrast to PneuNets, these grippers do not need an air supply, which makes them easier to use in environments like space or underwater. Since the first fin ray gripper was developed, you can now find them online, ready to be 3D printed, or even in toy shops!
Materials that can Memorize a Shape
What if we want to make a gripper that does not need motors or air pumps? Luckily, there is a never-ending sea of wild and wacky materials in soft robot research, and one popular type has a “memory” of its previous shapes. If you have ever wondered if a piece of metal or plastic could remember what it looked like when it was made, well, some of them can (Figure 2D). Metals that can do this are called shape memory alloys (SMAs) and such plastics are called shape memory polymers (SMPs).This shape recovery process can be used to bend grippers in the desired way by heating them up. There are many SMA and SMP soft robots being researched. Some of these grippers are even used in applications where the object is already hot, which means the SMA gripper only needs to get close to the object, and it will bend and grasp the object by itself.
Not all environments are hot or cold enough for SMA soft grippers to change shape, but luckily we can heat things with an electric current. By hooking up some wires to an SMA soft gripper, we can control the bending and recovery of the materials easily.
To Be As Sticky As Gecko Feet...
Geckos can climb on smooth surfaces, including glass, and stick to ceilings as if gravity does not exist. What makes their feet so special? It turns out they defy gravity by having really tiny structures on their feet. When in contact with walls (Figure 2E), these microscopic structures generate weak molecular-level sticky bonds called Van der Waals forces, which, when multiplied across many points of contact, become large enough for geckos to cling to ceilings. Since humans can now make very small things, we have replicated these structures [1] and even produced tape rolls with these sticky surfaces. We can create soft grippers with many contact points on which we attach artificial gecko skin, leading to a stronger grip and new ways for soft robots to interact with the world.
Can You Build a Soft Gripper at Home?
In cartoons like Doraemon, characters sometimes have balls as hands but seem to pick things up with no problem. Their hands look just like a soft gripper called a jamming gripper. The physical principle behind these grippers is simple. You take a bunch of small items like beads, rice, powders, or coffee beans, put them in a bag, and suck all the air out from between them. The floppy bag then freezes in place, becoming a unique solid object and trapping any object you might have pressed into it. You may have seen this principle when you open packet of coffee grounds or vacuum-packed rice; when you buy it at the supermarket, it is pretty solid, but when you open it and the air goes inside, it becomes floppy. Perhaps some scientists who loved their coffee made the first jamming gripper by filling a balloon with their favorite coffee beans. With just a few household items (coffee, a balloon, a piece of tubing, and a vacuum cleaner) you can easily follow in their footsteps and make your own jamming gripper (Figure 3). The coffee-filled balloon is just like the round hands of those cartoon characters; you can press it onto something, vacuum out the air, and pick the object up.
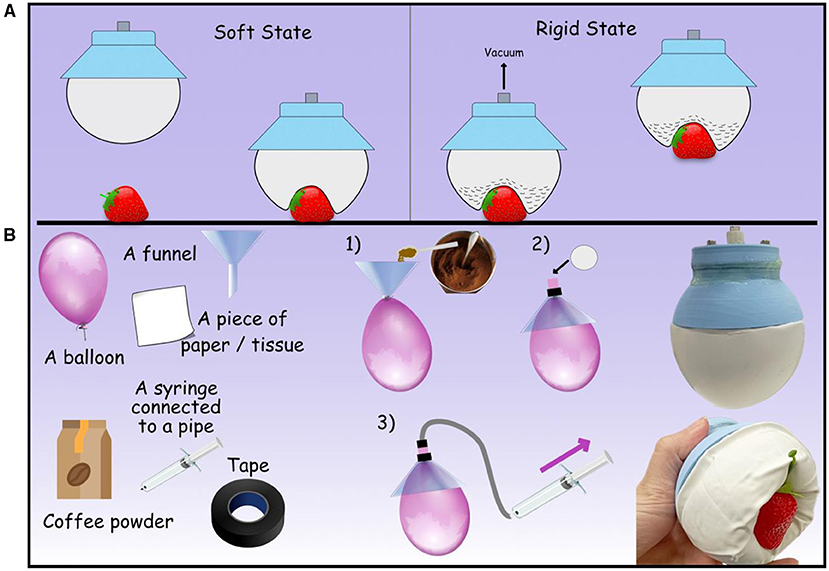
- Figure 3 - (A) In its soft state, the jamming gripper can adjust its shape according to the object’s shape.
- Applying the vacuum, the gripper hardens and can grasp the object. (B) To make one you need: a balloon, a funnel, paper/tissue, tape, coffee grounds, and a syringe connected to a tube. (1) Fill the balloon with coffee using the funnel. (2) Pull the balloon’s neck through the funnel and secure with tape. Attach the fabric/tissue to the balloon opening to keep the coffee in. (3) Connect the tube to the syringe with more tape. You are ready to test your jamming gripper!
Wrapping Things Up
We could talk about soft grippers for hours! If you are still curious and want to learn even more about soft grippers, check out [2]. And also if you want to know if one is better than others check out [3]. In summary, lots of exciting new soft robots and grippers are out there, born from a combination of natural inspiration and human engineering. The future is already among us; we just need to look with an open mind.
Glossary
Soft Grippers: ↑ A device made of soft materials (like rubber) that acts as the hand of a robot, allowing the robot to grab objects gently.
Continuum Robots: ↑ Robots that can bend in many ways because they have a large number of joints or soft material along their body (also known as large degrees of freedom).
Pneumatic Networks: ↑ A soft gripper design with a special arrangement of air pockets, powered by pressurized air. This design allows the finger to bend when pressurized.
Fin Ray Effect: ↑ Inspired by fish fins, the fin ray effect describes a bone structure that bends toward an applied force instead of away from the force.
Shape Memory Alloys: ↑ Alloys are mixtures of different metals. With the correct composition and creation, they can have a defined shape that is programmed in their structure.
Shape Memory Polymers: ↑ Polymers are long structured chains of molecules, like plastics. Some have shape memory effects, meaning they can remember their shapes even after being squeezed, with a little bit of heat.
Van Der Waals Forces: ↑ Weak, temporary attractions between molecules that hold them close together. These forces are not as strong as chemical bonds but help things like water drops and gecko feet stick to surfaces.
Jamming Grippers: ↑ Grippers that use materials that change from a soft, liquid-like state to a solid when air is removed. This makes them rigid, allowing them to grip and hold objects securely.
Conflict of Interest
The authors declare that the research was conducted in the absence of any commercial or financial relationships that could be construed as a potential conflict of interest.
Acknowledgments
This work was supported by the EPSRC grants EP/V062158/1 and EP/V026518/1.
References
[1] ↑ Autumn, K., and Gravish, N. 2008. Gecko adhesion: evolutionary nanotechnology. Philos. Trans. R. Soc. A Math. Phys. Eng. Sci. 366:1575–1590. doi: 10.1098/rsta.2007.2173
[2] ↑ Shintake, J., Cacucciolo, V., Floreano, D., and Shea, H. 2018. Soft robotic grippers. Adv. Mater. 30:1707035. doi: 10.1002/adma.201707035
[3] ↑ Terrile, S., Argüelles, M., and Barrientos, A. 2021. Comparison of different technologies for soft robotics grippers. Sensors 21:3253. doi: 10.3390/s21093253