Abstract
Many animals, such as elephants and octopuses, can change the stiffness of their limbs and trunks. This allows them to move around their environments as well as grab things and move them around. We would love our soft robots to be able to do the same! We can do this using a technique called jamming, in which the materials in the trunk are packed together to change its stiffness. Jamming has been used in all sorts of soft robots, like robotic hands for gently picking up fruits and vegetables, exoskeleton suits, and surgical instruments. In this article, we will talk about the three main types of jamming that are used in soft robotics, and show how they can be used in real life. And guess what? At the end of the article, we will describe the use of jamming to build a robotic elephant trunk that can change its stiffness, just like a real elephant’s trunk!
What are Soft Robots?
Soft robotics is a field in which robots are made from soft materials instead of hard ones. Soft robotics scientists use things like silicone, rubbers, and gels, which let robots change shape similar to the way living creatures can bend and stretch. Think of Baymax, the friendly inflatable healthcare robot in Big Hero 6 — that is a soft robot!
Some of the most useful soft robots are based on real animals. Soft robots therefore need to copy what real animals can do. This means being flexible so they can move well, pick up objects, and interact with the world. For example, an octopus tentacle or an elephant trunk does not have bones but can become stiff when needed. Think of an elephant picking up food with its trunk (Figure 1)[1]. An elephant’s trunk has over 90,000 bundles of muscle fibers, which let it control the trunk precisely to grab food [2] and use tools (like a branch) to scratch its body [3]. The complex network of muscles in the trunk work together by relaxing and contracting (shortening) to produce forces that move the trunk. The tips of their trunks have finger-like features, which they can stiffen to grab onto food before bringing it to their mouths [4]. In soft robotics, we use a method called jamming to allow robots to harden themselves, similar to what elephants do with their trunks.
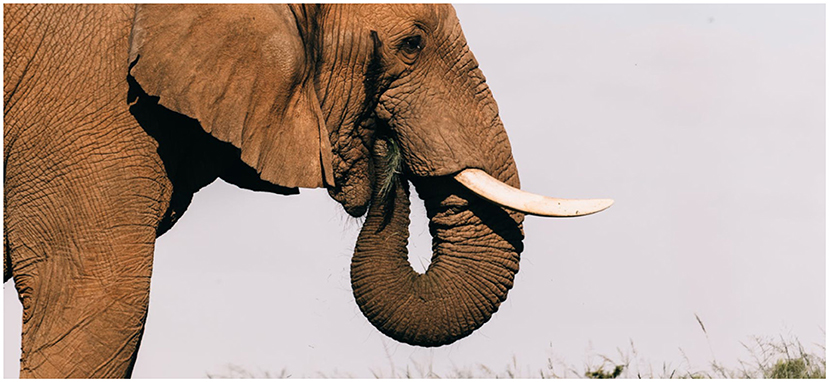
- Figure 1 - Elephant trunks are normally flexible, but they can also stiffen to grab onto food or other objects.
A Brief Introduction to Jamming
Jamming allows robots to both change shape and change their stiffness. The robot can be unjammed, which makes the robot flexible for moving and exploring, or jammed, which makes the robot rigid and great for gripping. Next, we explain how the most popular jamming methods work. Then we will put theory into practice and describe how to make a soft elephant trunk!
Granular Jamming
Imagine you are in the supermarket, and you reach for a bag of beans. The vacuum-packed bag feels hard and rigid, with all the beans packed closely together in one solid block. Beans and grains sold in supermarkets are often vacuum sealed to ensure a longer shelf life. This is done by removing the air inside the package to prevent the growth of bacteria and to reduce the size of the package for transport and storage.
After buying the beans, you decide to tear the bag open. The seal holding the vacuum is broken and air returns into the bag. The bag feels a lot more compressible, and the beans can move freely, shifting around inside the bag when you squeeze it. This phenomenon is known as granular jamming, in which particle materials such as coffee grounds, beans, rice, gravel, and sand can reversibly change from a fluid-like state to a solid-like state when a pressure is applied [5]. When the granular substances can flow freely, the robot is soft and flexible. However, when a vacuum pressure is applied, these grains are compressed by a membrane and have nowhere to move, and hence they form a solid structure.
Layer Jamming
You can imagine layer jamming like making a sandwich! Instead of using normal bread, we use flat materials like stacks of paper or plastic sheets. We put these layers in an envelope or bag, similar to wrapping up a sandwich. If you do not wrap your sandwich tightly, the ingredients inside can spill out, so the wrapping needs to be tight enough to hold them in place. That is what we do in layer jamming—we compress these layers together using a vacuum, to create a rigid structure and stop the layers from sliding against each other. When unjammed (at normal pressure), the layers are free to slide and move against each other, because there are still air gaps between the layers (Figure 2). However, once a vacuum is applied to jam the structure, air is sucked out and the envelope forces the layers together, compressing the “sandwich” structure. The space between layers, which was previously occupied by air, shrinks down, and the layers pack tightly together. As more vacuum pressure is applied, the layers become closer and closer together, and the area of contact increases. The friction between the layers therefore prevents the layers from sliding against each other, effectively immobilizing the entire structure. The structure therefore becomes entirely rigid, like a solid block, which is difficult to bend.
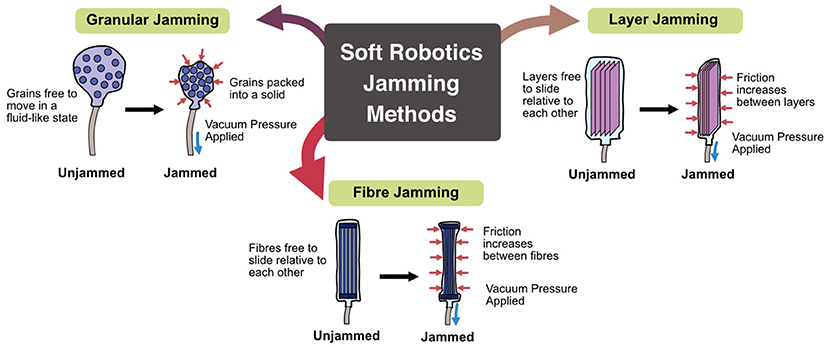
- Figure 2 - The three main jamming methods used in soft robotics.
Fiber Jamming
Fiber jamming structures use of bundles of fibers enclosed within a cylindrical envelope (Figure 2). They are a bit like muscle fibers wrapped together by connective tissue sheaths. These fibers could be made of materials such as plastic, silicone, waxed cotton, and even leather [6]. When unjammed (at normal pressure), fibers in the bundle are free to slide against each other. However, when a vacuum is used to remove all the air, these fibers are forced together by the envelope, which increases contact area and friction between the fibers, and consequently increases their stiffness. This is similar to how muscles in the human arm tighten up and stiffen when we lift something heavy.
Jellyphant: A Granular Jammed Elephant Trunk
Now we will explain how we built a simple, soft robot based on jamming (Figure 3A). In this case, we used granular jamming to build a soft robot that mimics some characteristics of an elephant’s trunk. Jamming has previously been used to make trunk-like robots with the freedom to move in many directions [7–10]. Additionally, granular-jamming systems can often be replicated at home, using easily available grains and a bit of creativity (or 3D printing if you are lucky enough to own a printer!). The membrane can be a balloon or a few wraps of cling film or Glad wrap.
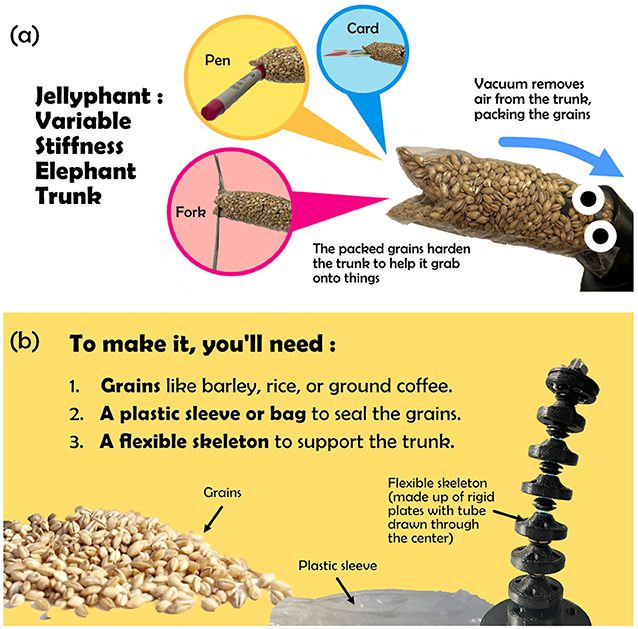
- Figure 3 - (a) Jellyphant, an elephant trunk-inspired soft robot capable of grabbing household objects, such as a fork, pen, and card, through granular jamming.
- (b) Jellyphant construction materials.
Because we could call this artificial trunk whatever we wanted, we decided to call it Jellyphant! Jellyphant was constructed with a flexible skeleton, barley grains, and a plastic sleeve (Figure 3B). Unlike real elephant trunks, which do not have any bones or cartilage, some soft robots still need structural support to avoid a phenomenon called buckling (unwanted bending). Soft robots are often prone to buckling when they try to support weight. As in the Jellyphant, a support structure like a flexible skeleton is often required to maintain the overall shape of the soft robot, to make sure its body does not become too floppy. The skeleton is made up of rigid plastic plates with spacers and a vacuum tube drawn through its center. The vacuum tube is connected to a home vacuum, through a small nozzle. A plastic sleeve was then stretched over the skeleton and filled with barley grains.
In its unjammed state, Jellyphant is soft and flexible, as the grains can move and shift within the membrane and around the skeleton plates. Jellyphant can be easily deformed with little force in this state. However, when the vacuum is turned on and the structure is jammed, the structure becomes rigid and can grab onto objects. Figure 3A shows Jellyphant grabbing onto household items like a fork, pen, or a piece of card! This is possible because, by jamming, the grains are packed tightly together around the object, and they lock the object in place.
Conclusion
In a variable stiffness robot, a flexible state is helpful for delicate tasks, keeping the people around the robot safe, and preventing damage to the robot. On the other hand, a rigid state is helpful when the robot needs to lift heavy things and stay in a specific shape. In summary, soft robots are incredibly versatile, and can change their shapes and functions more easily than traditional, rigid robots. In the future, the Jellyphant could be scaled up to create a bigger robot, which might be used to help in medical surgeries. Because these robots are soft and flexible, they can easily move through tight spaces and are less likely to harm the human body. These kinds of robots a called continuum robots, and they can be controlled using wires or cables connected to motors, kind of like a puppet on strings.
Soft robotics is an exciting field that is reshaping the way we understand, build, and interact with robots, and it has the potential to improve human lives. The future of soft robots looks pretty “solid”!
Glossary
Soft Robotics: ↑ An area of robotics that study the design, creation, and control of robots made of flexible materials.
Jamming: ↑ A process which enables controllable stiffness in soft robotics.
Granular Jamming: ↑ A process whereby granular particles in membrane pack-together and transition from a fluid to solid-like state after application of a vacuum.
Layer Jamming: ↑ A process whereby a stack of planar layers or sheets enclosed in a membrane are compressed together after application of a vacuum.
Friction: ↑ A force that resists motion of two surfaces sliding against each other.
Fiber Jamming: ↑ A process whereby a bundle of fibers in a membrane transitions from a flexible to rigid beam after vacuuming.
Continuum Robots: ↑ Long and continuous robots, with many joints to allow them to bend and twist like animals.
Conflict of Interest
The authors declare that the research was conducted in the absence of any commercial or financial relationships that could be construed as a potential conflict of interest.
References
[1] ↑ Manti, M., Cacucciolo, V., and Cianchetti, M. 2016. Stiffening in soft robotics: a review of the state of the art. IEEE Robot. Autom. Magaz. 23, 93–106. doi: 10.1109/MRA.2016.2582718
[2] ↑ Longren, L. L., Eigen, L., Shubitidze, A., Lieschnegg, O., Baum, D., Nyakatura, J. A., et al. 2023. Dense reconstruction of elephant trunk musculature. Curr. Biol. 33, 4713–4720.e3 doi: 10.1016/j.cub.2023.09.007
[3] ↑ Chevalier-Skolnikoff, S., and Liska, J. 1993. Tool use by wild and captive elephants. Animal Behav. 46, 209–219. doi: 10.1006/anbe.1993.1183
[4] ↑ Wu, J., Zhao, Y., Zhang, Y., Shumate, D., Braccini Slade, S., Franklin, S. V., et al. 2018. Elephant trunks form joints to squeeze together small objects. J. R. Soc. Interface 15, 20180377. doi: 10.1098/rsif.2018.0377
[5] ↑ Fitzgerald, S. G., Delaney, G. W., and Howard, D. 2020. “A review of jamming actuation in soft robotics”, in Actuators (Basel: MDPI), 104.
[6] ↑ Brancadoro, M., Manti, M., Tognarelli, S., and Cianchetti, M. 2018. “Preliminary experimental study on variable stiffness structures based on fiber jamming for soft robots”, in 2018 IEEE International Conference on Soft Robotics (RoboSoft) (Livorno: IEEE), 258–263.
[7] ↑ Clark, A. B., and Rojas, N. 2019. “Stiffness-tuneable limb segment with flexible spine for malleable robots”, in 2019 International Conference on Robotics and Automation (ICRA) (Montreal, QC: IEEE), 3969–3975.
[8] ↑ Santiago, J. L. C., Godage, I. S., Gonthina, P., and Walker, I. D. 2016. Soft robots and kangaroo tails: modulating compliance in continuum structures through mechanical layer jamming. Soft Robot. 3, 54–63. doi: 10.1089/soro.2015.0021
[9] ↑ Kim, Y. J., Cheng, S., Kim, S., and Iagnemma, K. 2012. “Design of a tubular snake-like manipulator with stiffening capability by layer jamming”, in 2012 IEEE/RSJ International Conference on Intelligent Robots and Systems (Vilamoura-Algarve: IEEE), 4251–4256.
[10] ↑ Cheng, N. G., Lobovsky, M. B., Keating, S. J., Setapen, A. M., Gero, K. I., Hosoi, A. E., et al. 2012. “Design and analysis of a robust, low-cost, highly articulated manipulator enabled by jamming of granular media”, in 2012 IEEE International Conference on Robotics and Automation (Saint Paul, MN: IEEE), 4328–4333.