Abstract
Drilling into the Earth is important for collecting resources like water and raw materials, and it is also done for scientific reasons, to learn about the planet. A method called rotary drilling is often used to drill holes deep into the Earth. To understand how deep we can drill, you need to understand how rotary drilling is performed and what the challenges are. This article explains how we drill deep holes and introduces the equipment needed for rotary drilling. The deeper we drill into the Earth, the higher the temperature and pressure. As temperature and pressure increase, drilling equipment will eventually fail. Another challenge is preventing the hole from collapsing. We will explain how these challenges can be tackled and how deep we can drill with current drilling techniques.
Why Drill Into the Earth?
Journey to the Center of the Earth is a classic science fiction novel published by Jules Verne in 1864, expressing human curiosity about Earth’s interior. We know little about the inside of our planet, and the only way to prove our theories is to drill. A common reason to drill deep boreholes into the ground is to access underground materials that we need, such drinking water, which is often near the surface, as well as oil, gas, and other raw materials found in deeper ground. Another reason for drilling is geothermal energy, which is an environmentally friendly type of energy that uses the natural heat of the Earth to produce electricity or to heat buildings. Scientists also drill into the Earth to learn more about the planet. See this article for more information on scientific drilling.
Deepest Holes in the World
So, how deep can we drill? In 1989, the Kola Superdeep Borehole in Russia reached a depth of 12,262 m, which remains the deepest we have ever reached into the Earth [1]. The German Continental Deep Drilling Program (KTB) was another scientific drilling project, carried out from 1987 to 1995, that reached 9,101 m [2]. Both projects tried to drill very deep for scientific reasons, but they stopped because of money and equipment issues.
How is Drilling Performed?
Rotary drilling is the most common method used to drill deep holes into the ground. The machine used to perform rotary drilling is called a drill rig (Figure 1), and it has many parts. On the drill rig, a tool called a drill bit is attached to the end of a hollow steel pipe called a drill string, which is rotated by a strong motor and pushed into the ground. As the drill bit turns, it makes a cylindrical borehole. To drill deeper, additional pipes are added to the drill string once the previous pipe is deep within the Earth.
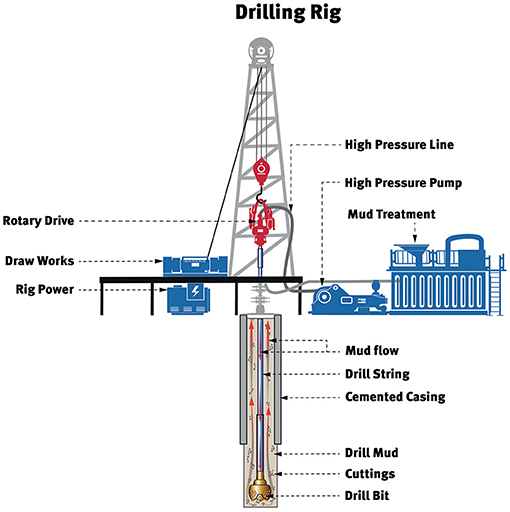
- Figure 1 - A drilling rig is a complex machine with many components.
- In general, for rotary drilling, a drill bit is attached to a drill string, which is rotated by a strong motor (rotary drive). Cuttings are removed from the borehole by pumping drill mud through the drill string. The casing helps to stabilize the borehole so that it does not collapse.
While drilling, the drilled rock pieces, called cuttings, must be removed from the borehole. This is achieved by pumping fluids called drill mud through the hollow drill string and the drill bit. The drill mud carries the cuttings from the bottom of the hole to the surface. The hole must remain stable during drilling so that it does not collapse, which can be achieved by proper drill mud management and good casing design. The casing is a heavy steel pipe that holds up the fragile wall of the borehole. It is usually fixed with cement to the borehole wall [3].
With every kilometer we drill into Earth’s crust, the pressure increases equal to the weight of a pony standing on an area of the size of a fingernail (an average of 280 kg/cm²) and the temperature increases by roughly 30°C. These conditions require very strong tools and materials. The hardness of the rock is another challenge—the harder the rock, the slower the drilling progresses and the faster the drill bits wear out. When bits wear out, we replace them by pulling up the entire string.
Drilling Rig Strength Determines How Deep We Can DIG
Several factors determine how deep we can drill. The first is the “strength” of the drilling rig, which depends on two main things: hook load capacity and hydraulic pressure capacity. Hook load capacity refers to how much weight the rig can handle. As we noted, the drill string is essential for drilling because it transmits energy from the rig to the bit and is the flowline for the circulating drill mud. The drill string rotates the bit, gives it weight, and guides it. The deeper the drilling goes, the longer and therefore heavier the drill string gets and the closer it gets to the rig’s hook load capacity. The weight of the casing must also be taken into account. Casing is usually heavier than the drill string. For example, in the KTB project, the heaviest drill string weight reached 358 tons, while the biggest casing section weighed 690 tons—close to KTB rig’s 800-ton hook load capacity (Figure 2). If the weight of the drill string or casing exceeds the drill rig’s hook load capacity, then a part of the rig can break, which could hurt people working on the rig and damage the equipment. In such cases, drilling activity must pause temporarily or even stop for good.
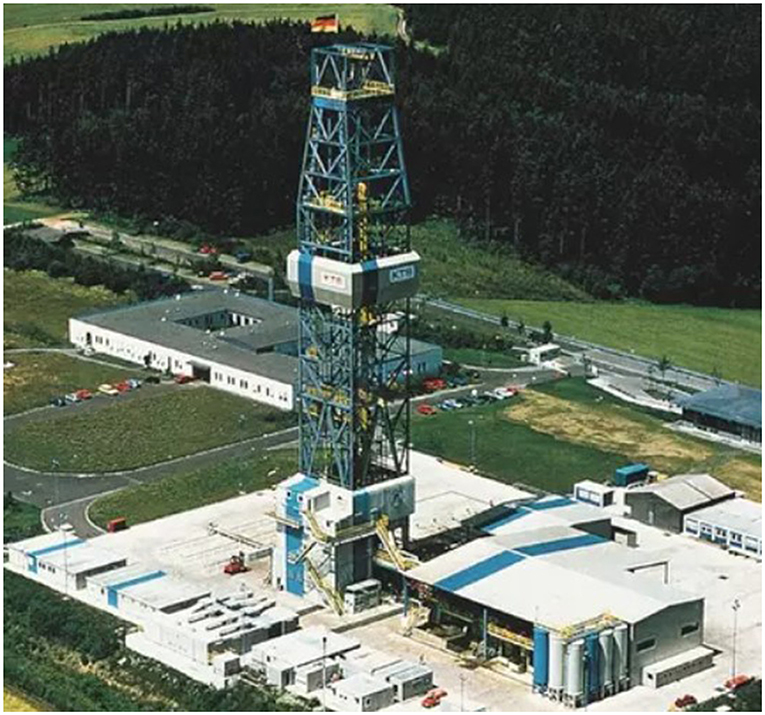
- Figure 2 - The KTB drilling rig in Germany.
- It has a hook load capacity of 800 tons and, between 1987 and 1994, it drilled one of the deepest scientifically used boreholes worldwide—at a depth of about 9,101 m. The drilling tower, called a derrick, has a total height of 87 m and marks the location of the borehole, which is directly below.
The second aspect of drill rig strength is hydraulic pressure capacity. This refers to the system’s ability to circulate drill mud. As we explained, drill mud removes the rock cuttings from the borehole by bringing them to the surface. Drill mud also rotates, cools, and lubricates the drill bit. High-pressure pumps push the drill mud from a tank system, through high-pressure lines, down the drill string to the bit. On the way from surface to the bottom, some of the pressure is naturally lost, but there must still be enough pressure left to bring the cuttings from the bottom to the surface, like a strongly flowing creek where the water flow is fast and strong enough to carry away sand grains. The power of the pump and the amount of pressure the equipment can handle set the drilling depths limits.
Other Limits to Borehole Depth
In addition to drill rig strength, there are some other things that affect how deep the borehole can get. One of these is borehole stability, which we mentioned earlier. The borehole must remain stable during drilling and, the deeper we drill, the more stress the rocks around the borehole walls are under. Eventually the borehole can collapse. This can be prevented by adjusting the properties of the drill mud. For example, drill mud density can be changed to balance the pressures between the drill mud and the fluids in the surrounding rocks.
Casing is also used to strengthen unstable zones while drilling, but the deeper we go, the more hostile the conditions of high temperature and pressure become, and more casing sections are required. The condition of the casing and drill string is another crucial aspect for successful drilling. In general, the deeper we drill, the more strain the drilling equipment is under and the greater the risk of equipment failures. A casing or drill string can easily break under its own weight when it gets too heavy.
To drill as deep as possible, we can choose specialized drill bits that best fit the conditions. In general, there are two main types of drill bits. Figure 3A shows an example of a roller-cone bit and Figure 3B shows a fixed cutter bit with diamond cutting elements. Regardless of what kind of drill bit is used, the bit must be pressed into the ground hard enough to cut through rock but not so hard that we end up bending the drill string. This is achieved by using heavy, thick-walled, hollow pipes, called drill collars, between the drill pipes and the bit. The drill collars in the drill string provide a force on the bit that can be fine-tuned from surface. This force is called weight on bit.
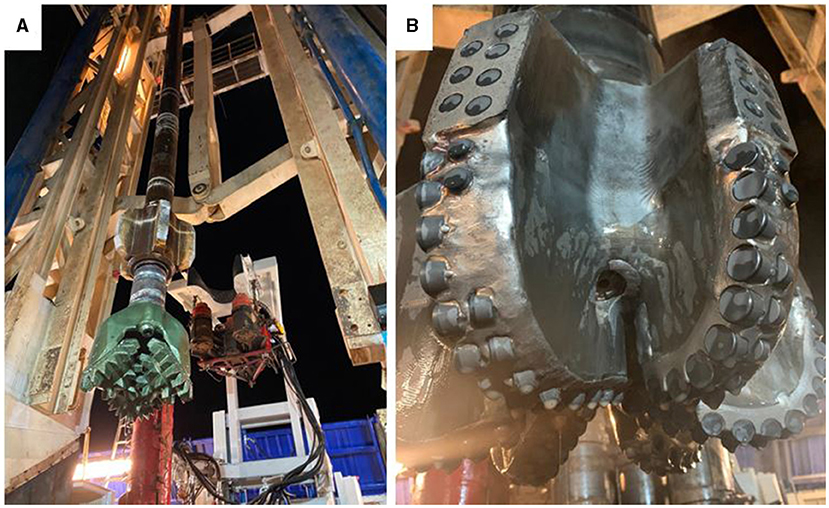
- Figure 3 - (A) A new milled tooth roller-cone bit installed on a drill string.
- This type (milled-tooth) is typically used for soft formations. Roller-cone bits are generally used to drill a wide variety of formations, from very soft to very hard. (B) A used fixed cutter bit with diamond cutting elements when pulled out of the borehole. This type of bits perform better in soft to medium-hard rocks, with low to moderate abrasiveness and hardness, and high homogeneity.
Can We Make Rigs to Drill Deeper?
As you can see, there are many technical factors that limit the depth to which we can currently drill into the Earth using rotary drilling. At a certain level of temperature and pressure, something is bound to give out! Technical advances may be able to increase the hook load capacity and hydraulic pressure capacity of the high-pressure pumps, but there will be a limit. The most important limiting factor is probably the sheer weight of the casing and the drill string, which will cause the drill string to break under its own weight. In the Kola drilling, special light-weight aluminum drill pipes were used, which allowed drilling to more than 12 km depth. But the Kola site had an advantage. Located in Northwestern Russia where the land is very cool, the temperature was still below 200°C even at 12 km depth. Technically, it might be possible to go slightly deeper than the Kola borehole—but only by a couple of km.
Drilling Deep for Science
Most drilling projects have no need to dig super deep into the Earth. For example, the mining and energy industries do not need to do so—they can get the products they need at easier-to-reach depths. Drilling super deep into the Earth is only interesting for scientific reasons. For example, drilling into the Earth’s mantle for the first time would be highly interesting for comparing the actual findings with scientists’ predictions of what that depth will be like. We could consider drilling into the mantle offshore, in places where there is “only” 5 km of water depth plus 5 km of seafloor to drill through before reaching the mantle. Such a project is technically possible. China’s newly built (2023) ocean drilling ship Mengxiang aims to be the first to reach Earth’s mantle offshore.
So, now you know why it is important to drill into the Earth and you have learned about some of the challenges that are faced while drilling to great depths. Even though there are depth limits with current drilling technologies, drilling projects are still important for collecting materials and studying the Earth. Hopefully, in the future, we will find ways to drill even deeper and learn even more about the planet we call home!
Glossary
Borehole: ↑ A deep, cylindrical hole made in the ground.
Rotary Drilling: ↑ A drilling method to drill deep boreholes. A drill bit installed at the end of a drill string is rotated and penetrates into the ground.
Drill Bit: ↑ A tool designed to make a cylindrical hole; in this case it is attached to the drill rig.
Drill String: ↑ A column of hollow pipes that carries drill mud into the borehole and helps to turn the drill bit.
Casing: ↑ A pipe that is assembled in a drilled section of a borehole that helps to make the borehole stable, so that it does not collapse.
Hook Load Capacity: ↑ The maximum force of the drill string and/or casing that a drill rig can carry or pull safely.
Hydraulic Pressure Capacity: ↑ The maximum force per area exerted by a fluid in a fluid-containing system. Exceeding the hydraulic pressure capacity causes the system to fail.
Drill Collar: ↑ A heavy thick-walled, hollow steel pipe that provides weight on bit for drilling.
Conflict of Interest
The author declares that the research was conducted in the absence of any commercial or financial relationships that could be construed as a potential conflict of interest.
References
[1] ↑ Helmut V. 1942. The Kola super-deep borehole SG-3 – first look at the deepest hole of the world. GeoJournal 9:431–2 doi: 10.1007/BF00171607
[2] ↑ Emmermann R, Lauterjung J. 1997. The German Continental Deep Drilling Program KTB: overview and major results. J. Geophys. Res. 102:18179–201. doi: 10.1029/96JB03945
[3] ↑ Mitchell RF, Miska SZ. 2011. Fundamentals of Drilling Engineering. Richardson, TX: Society of Petroleum Engineers. doi: 10.2118/9781555632076