Abstract
The cement industry is one of the largest polluters in the world, responsible for ~8% of all carbon dioxide emissions caused by human activity. Therefore, there is an urgent need to replace cement with another, more environmentally friendly material—something that is readily available and costs about the same as cement. Could table salt be this material? Our research group believes so, and we even proved it! Using salt from the Dead Sea, we used a simple, “green” process to form bricks made of 95% salt. These bricks can be formed in different shapes easily at room temperature. They are much stronger than similar concrete bricks and have additional advantages such as antibacterial activity and easy recyclability. Could these salt bricks be the building blocks of the future?
What is Cement?
Cement, which is a man-made building material, has a very ancient history. Starting millions of years ago, humans have created and used a wide variety of building materials and techniques. The first types of cement were developed to join stones and other building components together to make buildings stronger, and to protect dwellings from rain and other elements. However, the cement and concrete that we know today were not created until the Industrial Revolution, in the 1700s.
Although the chemistry of cement is well-known, it is still an important field of research [1]. The most common cement today, Portland cement (named after the type of stone quarried on the Isle of Portland in England) was developed in the 1800s, and is made mostly from two substances: calcium carbonate and silicates. When these materials are heated to a temperature of 1,450°C, a variety of compounds containing mainly calcium, silicon, and oxygen are created. The global cement industry produces more than four gigatons of cement per year, which is 4,000 million tons of cement—equivalent to the weight of a 20 cm-deep layer of water covering the entire state of Israel!
Cement Production Contributes to Climate Change
It is difficult to imagine a world without cement. Despite the enormous importance of this substance, when it comes to the environment, it was not such a great invention. Cement production is directly responsible for about 8%-9% of all carbon dioxide (CO2) emissions in the world. CO2 is a very significant greenhouse gas, which means that when it reaches the atmosphere, it directly contributes to climate change [2]. The cement industry is thought to be the second largest industrial polluter in the world today, for two reasons: first, the cement-making process takes place at very high temperatures, which requires a huge amount of energy. Second, the process produces CO2. In short, the creation of one cubic meter of concrete requires the same amount of energy found in about 40% of a barrel of oil!
To combat climate change, it is becoming increasingly clear that we must do more than transition to renewable energies like solar and wind. We must also replace fundamental materials that require enormous amounts of energy, such as cement and steel, with “greener” options [3]. But it is unlikely that the world will adopt a new material unless it saves industries money or unless it becomes a legal requirement—just as electric cars would not be on the roads today if lawmakers (starting in California USA) had not issued a formal order for their use. By doing so, lawmakers also created a financial reason for companies in the automobile industry to develop more electric vehicles. Could salt be used to produce a building material that costs about the same as cement, that is available in the same quantities, and that can be easily delivered?
Huge Salt Surpluses from the Dead Sea
A few years ago, Israel’s Ministry of the Interior asked the public to propose ideas for solving the problem of rising water levels in the southern part of the Dead Sea (here is an article about this call for proposals). The Dead Sea has two parts—a deep, northern part (more than 300 m deep in some parts)—the level of which is going down, and a southern part (both Israeli and Jordanian), the level of which is rising by about 20 cm every year.
This rise is caused by a process industries use to extract valuable minerals from the salt water. As part of this process, the seawater evaporates in huge ponds, leaving behind ~20 million tons of table salt (sodium chloride) per year on the Israeli side. After the table salt sinks, the remaining water is transferred to other ponds, where the desired minerals are crystallized. The salt that sinks creates a bottom layer that pushes the water up, causing the water level to rise. Water is even starting to rise to the level of the hotels in the southern part of the Dead Sea.
Can Salt be Used in Place of Cement?
In their ad, the Ministry of the Interior appealed to the public for ideas about what could be done with huge amounts of salt (people do not eat this salt because it is too bitter). When Daniel read the announcement, he soon thought about the huge amounts of materials used by the construction industry, and wondered whether it would be possible to use table salt to make building bricks. At first, this idea did not seem possible because we know that table salt dissolves in water. But this idea is not entirely new. In various places, such as in the Sahara or the Salar Deserts (Figure 1), buildings are built from salt—and when it rains once every few years, they are rebuilt. However, this is not a practical solution for countries that have wetter climates.
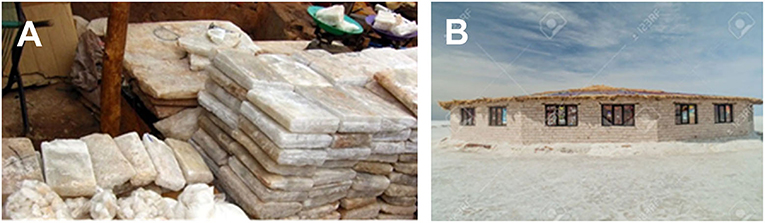
Then he wondered if we could compress the salt into bricks and coat them with a sealant—something that would not let water through. When we tested this, though, it turned out that we did not even need the sealant. By compressing the salt (after grinding it and adding some relatively simple ingredients) we created an unusually strong salt brick that is significantly less soluble than salt is in its natural state.
Creating and Testing Salt Bricks
The entire process of making salt into bricks [3] has three simple steps: (1) creating the mixture by combining 95% Dead Sea salt with 5% other ingredients; (2) grinding, which determines how smooth the surface of the bricks will be; and (3) compression of the bricks at a pressure of 2 tons/cm2. The main advantage of this method is that it has a very low carbon footprint, meaning it does not release a lot of greenhouse gases. Everything is done at room temperature, and the bricks are ready immediately. Compression is carried out in a mold made of stainless steel, since salt causes corrosion of metals such as iron. Figure 2 shows some of the bricks we made.
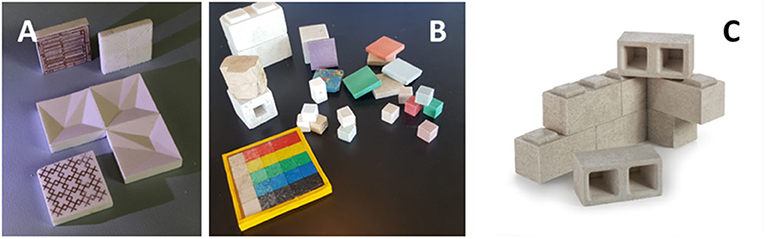
- Figure 2 - Products of the method we developed.
- (A) Salt tiles prepared in one step by compression against 3D surfaces. (B) Objects made of salt, to which food coloring was added before compression. (C) The size of the salt bricks is 5 cm × 5 cm × 10 cm.
We conducted many experiments to test the properties of the bricks, including how resistant they were to various humidity and temperature conditions; how strong they were; how difficult it was to drill into them; how they fit together, and more (Figure 3).
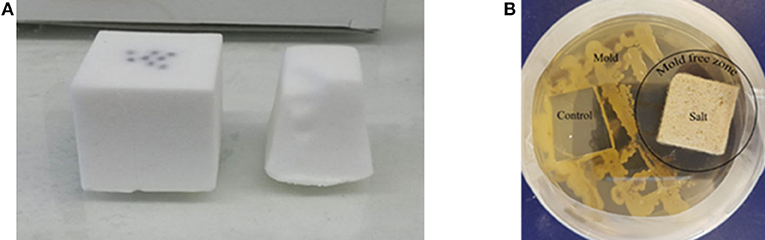
- Figure 3 - (A) Two salt cubes after 30 min of immersion in water.
- The cube on the left was prepared by our three-step compression process, while the one on the right was made without additives. You can see that compression and the addition of a small amount of other material (5%) dramatically affect the solubility of the salt brick. (B) No colonies of fungus (mold) grew around the salt cube in the petri dish because salt pulls the water out of living cells, preventing their growth.
We discovered that, when our salt bricks are exposed to high humidity, they absorb moisture; but when the humidity is lowered, the bricks release the moisture back into the environment. Therefore, a room lined with salt bricks on the inside will maintain a low and relatively constant humidity. Additionally, we found that salt bricks prevent the growth of bacteria and fungus because salt pulls the water out of living cells, preventing anything from growing on the surface of the bricks. Maybe salt tiles could be used to line interior walls in hospitals, to prevent the growth of microorganisms and keep patients safer.
What’s Next?
Our research raises many questions: Is it really possible to replace cement-based bricks with salt? Is the solubility low enough that the bricks will not dissolve? How much would these salt bricks cost to produce? Is there enough salt to make all the bricks we would need? How can construction companies be persuaded to switch from the concrete bricks they have been using for more than 150 years?
Fortunately, there are huge amounts of salt in Israel and other locations. The 20 million tons of salt that sink every year in the Dead Sea’s southern basin could easily cover Israel’s needs, for example. There is also salt leftover from various industrial activities, such as desalination of water. Normally, this process releases salt into the sea, damaging the enviroment and going against the Barcelona Convention, which aims to protect the Mediterranean Sea. In many places, including Germany, the United States, Spain, and Belarus, there are actual mountains of salt—some of which are man-made.
Salt bricks have several positive qualities. First, salt is not toxic, flammable, or dangerous. In fact, it is quite healthy! In some countries including Israel, there are salt rooms designed for people suffering from breathing problems. Since the process for creating salt bricks is physical instead of chemical, the bricks can be ground back down into raw materials, allowing them to be simply and efficiently recycled.
So, what’s the problem? There are still two main hurdles to developing salt bricks for construction. First, the construction industry does not change quickly—it is well-known that it takes the industry years to start using a new material. Second, if lawmakers do not push for the replacement of cement with another material such as salt, the chance that a company will do so on its own is extremely slim. Commercial companies are unlikely to undertake any project aimed at preserving the planet unless they have a financial reason to do so as long as there are no laws or financial incentives. We believe that eventually and due to publish concern and pressure, cement will be replaced where salt seems to be a very appealing candidate.
Glossary
Cement: ↑ The material used as a binder to hold all the components of construction elements, such as bricks.
Concrete: ↑ A construction material that gets hard and very strong by mixing cement, aggregates and water.
Greenhouse Gas: ↑ A gas that prevents some of the Sun’s heat that reaches Earth from being emitted back into space, thus increasing Earth’s temperature and causing global warming.
Soluble: ↑ Able to dissolve in a liquid, breaking down into tiny basic units and resulting in a clear solution.
Carbon Footprint: ↑ The environmental impact of industrial processes processes, mainly having to do with the release of greenhouse gases.
Corrosion: ↑ A chemical process in which a metal reacts with oxygen from the air, usually in the presence of water, and loses its metallic properties as a result.
Humidity: ↑ A measure of the amount of water vapor in the air, which depends on the temperature.
Desalination: ↑ A process of removing the different salts from the sea or other salted waters.
Conflict of Interest
The author declares that the research was conducted in the absence of any commercial or financial relationships that could be construed as a potential conflict of interest.
Acknowledgments
Figure 1A was taken from: https://www.worldhistory.org/image/10161/salt-slabs-timbuktu/. Figure 1B was taken from: Phil Whitehouse - https://www.flickr.com/photos/philliecasablanca/2052678622/.
References
[1] ↑ Shi, C. J., Jimenez, A. F., and Palomo, A. 2011. New cements for the 21st century: the pursuit of an alternative to Portland cement. Cem. Concr. Res. 41:750–63. doi: 10.1016/j.cemconres.2011.03.016
[2] ↑ Andrew, R. M. 2018. Global CO2 emissions from cement production. Earth Syst. Sci. Data 10:195–217. doi: 10.5194/essd-10-195-2018
[3] ↑ Afrin, H., Huda, N., and Abbasi, R. 2021. An overview of eco-friendly alternatives as the replacement of cement in concrete. IOP Conf. Ser.: Mater. Sci. Eng. 1200:012003. doi: 10.1088/1757-899X/1200/1/012003